混凝土離析原因及危害
離析是混凝土經(jīng)常產(chǎn)生的現(xiàn)象,其在離析后在泵送過程中容易導致堵管、爆管,澆筑在模板時容易發(fā)生結構分離,上面會出現(xiàn)砂漿層,混凝土的表層也容易出現(xiàn)蜂窩、麻面、空洞等質(zhì)量問題。怎樣做好防止和解決混凝土出現(xiàn)離析是其工作人員必須要重視的工作,進而能夠提升混凝土項目的質(zhì)量。
1、離析的危害
1.1影響混凝土的泵送施工性能,造成粘罐、堵管、影響工期等,降低經(jīng)濟效益。
1.2影響混凝土結構表觀效果,混凝土表面出現(xiàn)砂紋、骨料外露、鋼筋外露等現(xiàn)象。
1.3使混凝土強度大幅度下降,嚴重影響混凝土結構承載籠力,破壞結構的安全性能,嚴重的將造成返工,造成巨大的經(jīng)濟損失。
1.4混凝土的勻質(zhì)性差,致使混凝土各部位的收縮不一致,易產(chǎn)生混凝土收縮裂縫。特別是在施工混凝土樓板時,由于混凝土離析使表層的水泥漿層增厚,收縮急劇增大,出現(xiàn)嚴重龜裂現(xiàn)象。
1.5極大地降低了混凝土抗?jié)B、抗凍等混凝土的耐久性能。
2.混凝土離析原因
混凝土離析是指拌合物組成材料之間的粘聚力不足,拌合物成分相互分離,粗集料下沉、砂漿上浮,以致造成混凝土硬化后出現(xiàn)蜂窩、麻面、薄弱夾層等質(zhì)量缺陷的現(xiàn)象。
導致混凝土出現(xiàn)離析主要有六大原因:
一、水泥:
水泥質(zhì)量的穩(wěn)定直接影響著混凝土質(zhì)量的穩(wěn)定,水泥質(zhì)量的變化有可能會導致混凝土出現(xiàn)離析。
1、水泥細度的變化:水泥細度越高,其活性越高,需水量也越大,水泥顆粒對減水劑的吸附能力也越強,能明顯減弱減水劑的減水效果。因此,當水泥細度突然降低時,外加劑的減水效果會明顯增強。此時,如果外加劑摻量不變,混凝土的用水量將大幅度減少。如果不及時調(diào)整,容易造成外加劑用量過大,產(chǎn)生離析。
2、水泥含堿量的變化:堿含量對水泥與外加劑的適應性影響很大,含堿量降低,減水劑的減水效果增強。當水泥的含堿量發(fā)生明顯變化時,可能對混凝土的黏度、流動度產(chǎn)生較大的影響,產(chǎn)生離析。
3、水泥保管與存放時間:水泥如果保管不好,極易受潮,受潮后需水量將降低。水泥存放時間越長,顆粒之間經(jīng)吸附作用互相凝結為較大顆粒,降低了水泥顆粒的表面能,削弱了水泥顆粒對減水劑的吸附,表現(xiàn)為減水劑的減水效果增強。如果不及時調(diào)整,容易造成外加劑用量過大,產(chǎn)生離析。
二、外加劑:
混凝土減水劑的摻量過大,減水率過高,單方混凝土的用水量減少,有可能使減水劑在攪拌機內(nèi)沒有充分發(fā)揮作用,而在運輸過程中不斷的發(fā)生作用,致使混凝土到現(xiàn)場的坍落度大于出機時的坍落度,產(chǎn)生離析。
三、粉煤灰:
粉煤灰是混凝土重要的摻和料之一,能極大改善混凝土和易性、密實性及強度性能。如果粉煤灰質(zhì)量波動較大,則混凝土質(zhì)量控制的難度增大,容易產(chǎn)生離析。
1、當粉煤灰的質(zhì)量突然變好時(如細度從19%變?yōu)?%),粉煤灰的需水量降低很大,容易造成混凝土出現(xiàn)離析。
2、當粉煤灰的質(zhì)量突然變差時(如細度從19%變?yōu)?8%),由于粉煤灰的很大一部分已失去膠結料的功能,因而外加劑相對膠結料摻量實際上是提高了,容易出現(xiàn)離析。
四、骨料:
骨料是混凝土中用量最大的材料,其質(zhì)量直接影響混凝土的質(zhì)量。骨料質(zhì)量的波動很容易造成混凝土的離析。
1、粗骨料粒徑增大、級配不合理、級配單一會產(chǎn)生離析。
2、砂子中片狀石屑量過大將影響混凝土的和易性,產(chǎn)生離析。
3、骨料的含水率過高,混凝土拌合料在攪拌機中攪拌時,骨料表層毛細管中的水不能及時釋放出來,容易使拌合水用量過大。而在運輸過程中,毛細管中的水不斷的往外釋放,產(chǎn)生離析。
4、骨料含泥量過大將使水泥漿同骨料的粘結力降低,對骨料的包裹能力下降,導致骨料分離,產(chǎn)生離析。
五、施工:
混凝土運送到施工現(xiàn)場后,工人隨意向拌和物中加水,導致水灰比增大,水泥砂漿變稀,拌和物的粘聚性變差,產(chǎn)生離析。
六、罐車:
混凝土罐車未將洗罐余水倒盡,致使混凝土送入罐車后水灰比發(fā)生變化,拌和物變稀,產(chǎn)生離析。
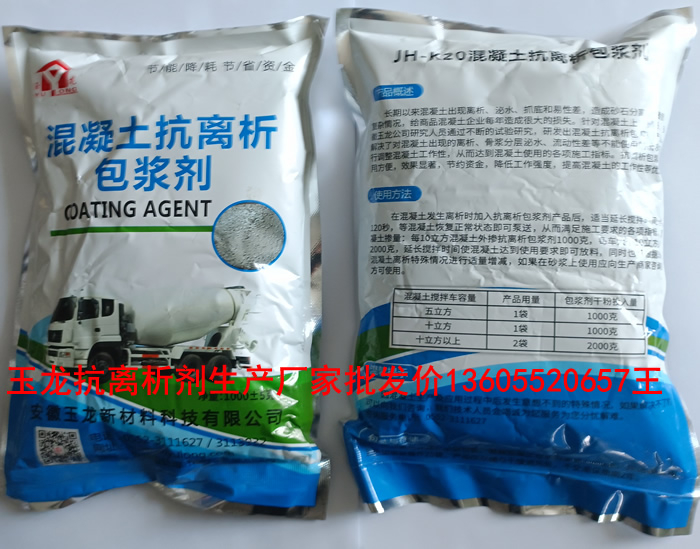
管理員
該內(nèi)容暫無評論